Are Indian cars rust proof
Over 30 lakh people get injured and hurt to life-long disabilities every year due to road accidents.
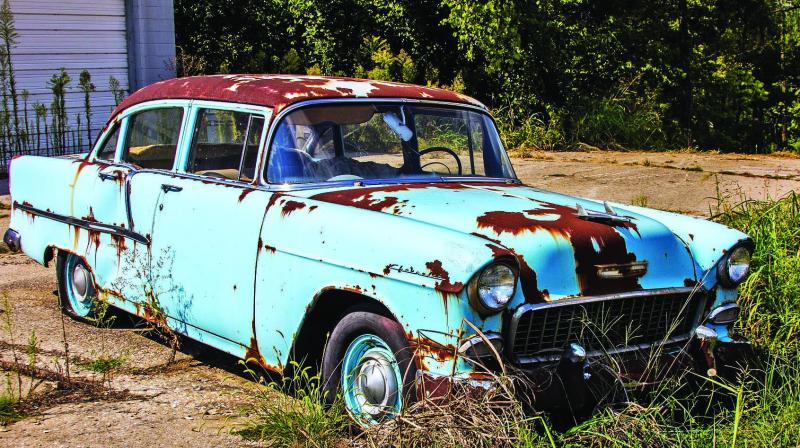
The safety of passengers in cars is generally measured by the presence of seat belts, airbags, crumble zone and shock absorbing capacity. But it is important to note that more than 50% of the total weight of an average vehicle globally is of Steel. And if this Steel is not galvanized – to prevent vehicles from corrosion and rust – this certainly would impact the safety of vehicles, safety of passengers, bring down the value of vehicles and increase life risk. Knowing this, should the steel used not be galvanized compulsorily is the question, and why not.
Despite being a state of art engineering with finest mobility revolutions, the automobile industry also has a flipside due to people losing lives in road accidents. Around 10 Lakh people lose life every year in road accidents around the world. Over 30 lakh people get injured and hurt to life-long disabilities every year due to road accidents.
As per IIHS (Insurance Institute for Highway and Safety) - death percentage in case of smaller and compact cars is twice when compared to bigger sedans and vehicles.
Ironically, the middle-class buys vehicles that are meant to be used for minimum 7-10 years and the steel used in most of these vehicles is not galvanized. Rather, the high-end class buys vehicles for just 2-4 years and these luxury vehicles use only galvanized steel. Safety is compromised in a larger section of society.
There is also a disparity by Indian automobile makers. For the Indian car market, only 30% of steel used is galvanized, i.e. rust proof or corrosion resistant. Rather, when the same model is exported, almost 70% of the steel used is galvanized. This is only because in India neither we have norms to use galvanized steel in the automobile industry nor there is enough consumer awareness.
The Steel in Automotive Industry – An Outlook
The Indian automotive industry, world’s sixth largest in terms of both volume and value, is expected to grow around four times by FY 2026 with approximately 10 % CAGR for vehicle sales volumes. The passenger vehicle sales alone are set to increase significantly by the year 2020.
Considering that automobile industry consumes around 15% of the country’s total steel demand and steel makes up more than 50% of the total weight of an average vehicle, it might be an enormous opportunity for the Indian steel industry, but it also brings with it the responsibility of supplying only galvanized steel to the automobile industry for the safety of people and preventing automobiles from rust and corrosion. Steel is used for safety of structures, and why ignore galvanization of steel if it brings more stability to steel. Can the safety be compromised ?
Flat products, such as hot rolled, cold rolled and coated steel sheets, account for about 80% of steel products consumed by the auto makers. Steel is used for roof, chassis, wheels, brakes, exhaust and engine.
Steel comes in a variety of different grades with lightness increasing in proportion with the cost of manufacturing the material and making the parts. Manufacturers will often use more than one type of steel in a car – prioritising better steel where more reinforcement is needed.
Research on Galvanization of Car Bodies
Starting in the mid 1980’s, the American Iron and Steel Institute (AISI) and the three major car makers - General Motors, Ford Motors and Chrysler Corporation - jointly participated in several parking lot corrosion surveys of cars in Detroit, Michigan area. Based on the results of this survey, as well as pressure from consumer advocates like Ralph Nader, the car companies converted from cold rolled to galvanized and galvanile steel for the exterior, interior, and underbody parts. Improvements in base coat and clear coat paint technologies were also made concurrently. The results of subsequent surveys, after the introduction of galvanized steel, showed dramatic improvements which heralded the car companies issuing 10+ year warranties against corrosion starting in the mid 1980’s. Europe, Japan and South Korea soon followed the North American decision to use galvanized sheet steel for the entire car body.
In the summer of 2015, an extensive study of automotive body corrosion was conducted in Mumbai area by IIT Bombay to track corrosion performance of currently used materials in Indian made cars costing less than Rs. 10 Lakhs. The study used similar methodology as used in North America to check for visible perforations, paint blisters, and surface red rust. The survey was conducted in several coastal and other humid regions of Mumbai. The results were surprisingly similar to those seen in the Detroit, Michigan Survey despite the fact that no road de-icing salts are used in Mumbai. The IIT report proved that there is a corrosion problem affecting the durability and the eventual safety of cars in India.
Indian car manufacturers use bare cold-rolled steel and its variants, while abroad, it is mandatory for auto companies to use galvanized steel bodies.
Tata Steel, POSCO Maharashtra & JSW all have the facilities to produce exposed quality galvanized or galvanile sheet to supply the automobile companies in India. There are no constraints in meeting the exposed quality steel demand required to convert all the parts from cold rolled to galvanized steel.
Rusting – Understanding Corrosion – function of Zinc
To understand, rusting is the common term for corrosion of iron and its alloys. Corrosion is the reaction of iron and oxygen, as may be present in water or air moisture. Any iron material when exposed to both oxygen and water is bound to rust - unless a preventive coating is applied on to it.
For coastal areas - due to higher moisture - rusting is a common phenomenon on iron & steel products. Additional is the sea water proximity - the presence of salt acts as a catalyst, accelerating the corrosion chemical reaction process.
Galvanized steel is protected because there is a protective Zinc coating on it. The Zinc functions in two ways after binding to the steel: first, it protects the metal from the atmosphere, and second, it provides cathodic protection.
Galvanizing stainless steel is popular because it has a low initial cost and it requires little maintenance throughout its lifetime. In addition, the ease of application is something that’s very appealing to steel suppliers. That’s an incredible value, especially when you consider that corrosion and rust costs the U.S. economy billions of dollars every year.
India too loses about 4-5% of GDP every year on account of losses due to corrosion.
Story of Indian Car Makers
However, with reference to cars - there are enough corrosion resistant coatings applied by car manufacturers globally in all critical areas, including body panel and underbody of car, to prevent rust. Galvanized material with rust resistant alloys and preventive coatings are measures used in cars to provide long lasting output without any corrosion.
When Indian car makers export the same model, it is galvanized since a number of countries have set norms for using only galvanized steel in automotive industry. But the same Indian car maker sells vehicles with not more than 30% galvanized steel to Indian customers, because they are not aware of it and neither any norms are set in India.
Unfortunately, five Indian prominent car models have got zero star ratings in crash tests conducted by the Global New Car Assessment Programme (Global NCAP). The results, released in New Delhi very recently, showed low levels of adult occupant protection in the five models. Global NCAP participated in a two-day conference on road safety hosted by the Institute of Road Traffic Education in Faridabad.
Can the Safety be Compromised - Corroded cars invite accidents
The safety of passengers in cars is generally measured by the presence of seat belts, airbags, crumble zone and shock absorbing capacity. Knowing that more than 50% of total weight of an average vehicle is of steel, how much that steel is galvanized is the question, and why not.
Experienced steel suppliers will tell you that galvanization is one of the best tools to protect steel from corrosion, but here are some more facts that might surprise you.
But if your car catches rust or corrosion, it is like termite, a cancer. If you detect it in initial stages, something can still be done. But if it is late, it actually reduces your car as junk. There are many parts in the car that are beyond the reach of regular check-ups and that is where the problem is more.
A small patch of rust or corrosion you see on your car isn’t just unpleasant to look at. Once rust lodges inside the microscopic holes in your car’s metal, it can also corrode and damage not just the surface, but also your car’s critical parts as well.
Rust can lead to brittleness and weaken metal over time. This can dissolve crumple zones that are designed to absorb energy in case of a collision. When this happens, then you and your family’s safety become compromised too.
There are three areas where rust can often be seen in a car.
First, it can be found on surfaces where the car’s paint has been chipped, thus, exposing the metal. Second, it can be found on the frame and chassis. Third, rust can be found on the trunk and engine parts, particularly in the intakes and connectors.
To add, despite being a state of art engineering with finest mobility revolutions, the vehicle also has flipside due to people losing lives in road accidents. Around 10 Lakh people lose life every year in road accidents around the world. Over 30 lakh people get injured or hurt to life-long disability every year due to road accidents.
History of Galvanization – The present context
Galvanized steel didn’t just appear out of nowhere. The term galvanization is named after Italian scientist Luigi Galvani. It is named such because it refers to any number of electrochemical processes, which happened to be Galvani’s specialty.
Galvanizing has evolved over the years. In current times, galvanization is more of an electro-deposition term than electro-chemical. And Zinc is the primary material used in the process. In recent years, science has allowed many new advances in the way metal is protected from the elements.
Global Studies on Rusting and Corrosion of Car Bodies
As per IIHS (Insurance Institute for Highway and Safety) - death percentage in case of smaller and compact cars is twice when compared to bigger sedans and vehicles.
In this race of building economical, affordable cars to have higher sales and better margins – some manufacturers are using economy grade material and this has come up when bodies like Global NCAP and Euro NCAP have released a report that some cars sold in India and other developing countries are so weak in body structure that even an airbag would be of no use.
Although – body weight on stand-alone basis does not signify how safe a car is. But – yes it does signify the probability of how strong the car is. The strong structural ability of the car comes with higher grade steel which is used in the car.
NACE International released the "International Measures of Prevention, Application and Economics of Corrosion Technology (IMPACT)" study, in which it estimated that the global cost of corrosion to be US$2.5 trillion, equivalent to roughly 3.4 percent of the global Gross Domestic Product (GDP). The two-year global study released at the CORROSION 2016 conference in Vancouver, B.C., examined the economics of corrosion and the role of corrosion management in establishing industry best practices. The study found that implementing corrosion prevention best practices could result in global savings of between 15-35 percent of the cost of damage, or between $375-875 billion (USD).
Looking beyond corrosion’s cost to businesses and industries worldwide, IMPACT assessed corrosion management practices across various industries and regions. Specifically, the study examined the oil and gas, pipeline, automobile industry and drinking & wastewater industries, as well as the U.S. Department of Defense.
Corrosion management systems (CMS) address the threat of corrosion for existing and future assets across the complete lifecycle of the asset, from design to decommissioning. The IMPACT Study notes CMS best practices for companies including: corrosion management systems that are integrated with organization policy overall; corrosion management information is made available to everyone within the organization and linked to its overall goals, and organizational leadership is actively involved in corrosion management decision making.
The study also identified the need for more corrosion management professionals. In fact, University of Akron in Ohio provides the only bachelor’s degree in corrosion engineering, with its first class graduated in 2015.
"There needs to be a renewed sense of priority for corrosion engineering amongst employers and educators," says Jim Feather, NACE International President. "NACE has provided training and professional development to tens of thousands of engineers and professionals in more than 130 countries, but the industry needs more academic programs and more universal means of communications across all levels of business."
Combating Rust and Corrosion in Automobile Sector - What can be done
A new BIS Standard for Automotive Steels is awaited. The proposed Standard will require car companies manufacturing cars in India to use one of several Zinc coated steel options for cars sold domestically. However, until this BIS Standard is released, car manufacturers are not obliged to use galvanized steel.
Immediate action points:
In the interest of passengers’ safety and also giving value to customers, there should be a minimum of 70% use of galvanized steel in the automotive industry.
To educate the importance of using rust-proof or corrosion resistant vehicles, the auto-insurance policy should also give weightage to standard of rust-proof or corrosion resistant vehicle.
This will not only reduce the junk being produced worth billions of dollars in India but would also set environment friendly norms for vehicles of next generation.
Cars – an Art of Engineering
Car-makers have to consider a range of factors when designing a car including weight, strength, perceived quality and ease of repair & construction. A car made of the most exotic materials might be incredibly strong and light, but it’ll cost a small fortune to produce. Manufacturers often need to use a mixture of materials in one car to achieve their goals.
Car is one among the finest Art of Engineering that has been introduced by Karl Benz by end of 19th Century. The finest mobility option is continually being improvised with modern features, styling with impressive performance and so far has reached a stage where almost 8.5 crore passenger cars are sold every year globally.
Cars are a well-crafted technology oriented machine, with a strong build and design. Though having side door beams and front crumple zones reduces the energy impact, but without a strong body structure – all is in vain. Car you own has strong shock absorbing body structure to absorb the energy force generated in the event of crash.
Your Lifestyle Drives Your Car – Protect from Corrosion
Your lifestyle is an important factor when it comes to your vehicle. Will you solely use your car for rugged purposes, like delivering goods in provinces? Or will you regularly drive it for outdoor trips? If you do, then you risk exposing your vehicle to hurling rocks, water, and uneven bumps on the road. And they all can chip away your car’s protective coating.
Rustproof protection is very much needed if you can’t clean your car regularly. A dirty vehicle, especially one with hardened dirt, tree sap, bird droppings, and even dead insects, can ruin your car’s paint. And when you leave them to dry up (and exposed to the sun’s heat), then they can corrode the metal and damage your car.
Although protecting body panels and vehicle frames against rust is important, the best rust inhibiting products also protect electrical areas such as battery terminals, wiring harnesses, switches and plugs from moisture. Keeping these areas protected
with the right type of product will greatly reduce repair costs and vehicle breakdowns. Lubrication of moving mechanical parts like brake cables, suspension components, and door hinges is another benefit of a good rust inhibitor/lubricant.
So if your car hasn’t succumbed to rust yet, there’s a good chance that galvanized steel is to be thanked for its long life.
Have a safe drive - be safe, for your-own-self and for your family.